Producing a Welding WPS: Step-by-Step Instructions for Professionals
Producing a Welding WPS: Step-by-Step Instructions for Professionals
Blog Article
Grasping Welding WPS Criteria: Best Practices and Techniques for Quality Welds
In the realm of welding, mastering Welding Procedure Requirements (WPS) requirements is a crucial part that directly influences the top quality and integrity of welds. As we browse through the complexities of welding WPS requirements, discovering vital insights and methods for achieving top-tier welds will certainly be critical for welders looking for to succeed in their craft and produce welds that stand the test of time.
Comprehending Welding WPS Requirements

Examiners depend on WPS documentation to confirm that welding procedures are being complied with correctly and that the resulting welds are of high quality. Designers use WPS criteria to make welding procedures that make sure the resilience and integrity of welded structures.
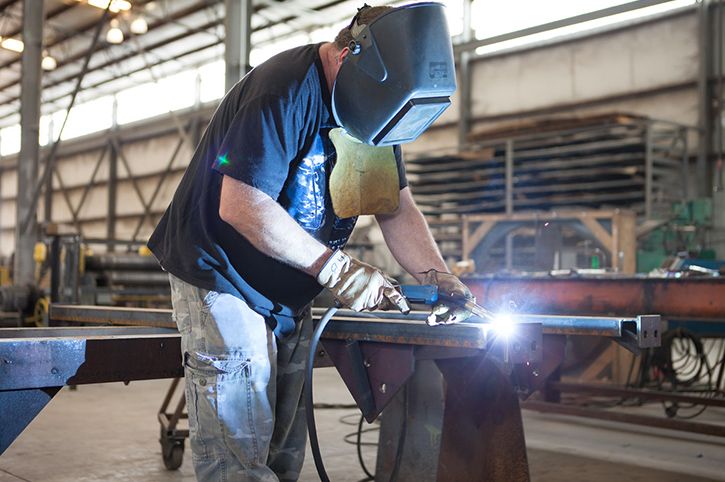

Important Tools for High Quality Welds
Grasping welding WPS standards is crucial for welders to successfully use the vital tools required for generating quality welds. The kind of welding machine required depends on the welding process being utilized, such as MIG, TIG, or stick welding. Wire brushes and breaking hammers are essential for cleansing the weld joint before and after welding to eliminate any kind of pollutants that can affect the top quality of the weld.
Key Methods for Welding Success
To achieve welding success, one should understand the key methods essential for creating high-quality welds. One important strategy is maintaining the right arc size. Keeping the electrode at the ideal range from the work surface is important for producing solid, uniform welds. Furthermore, managing the traveling speed is critical. Relocating also quickly can cause inadequate penetration, while relocating as well gradually can bring about excessive heat input and prospective issues. Proper control of the electrode angle is one more essential strategy. The angle at which the electrode is held can affect the bead shape other and penetration of the weld. Moreover, making certain consistent gun angle and direction of travel is vital for harmony in the weld grain. Last but not least, keeping a stable welding and a stable hand setting throughout the process is crucial to accomplishing precision and uniformity in the welds. By mastering these key techniques, welders can boost the top quality of their job and attain welding success.
Ensuring Compliance With WPS Requirements
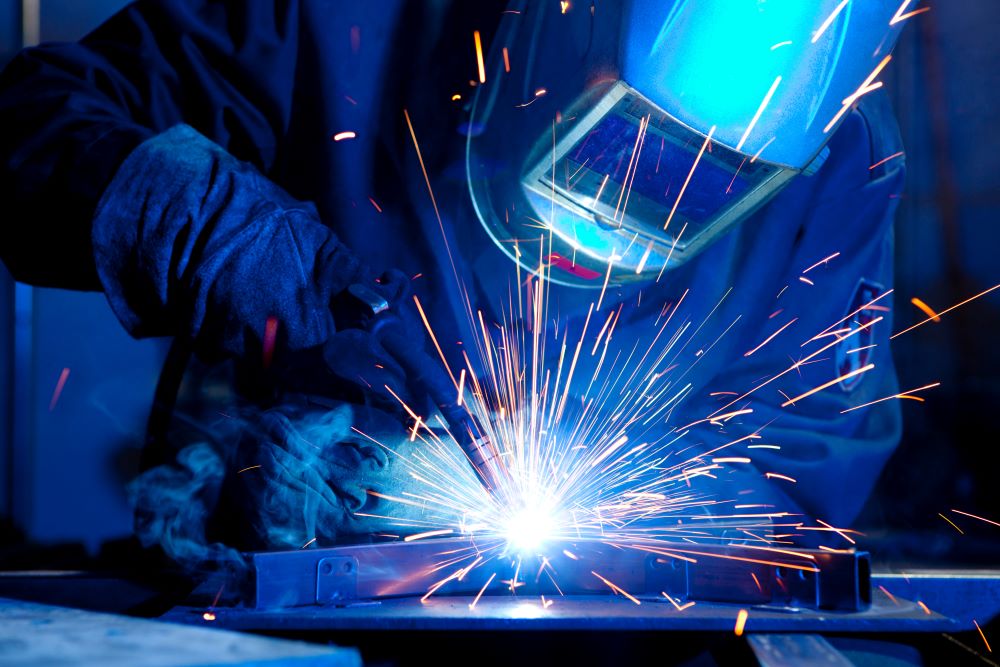
Moreover, welders need to go through training to familiarize themselves with the WPS requirements relevant to their job. Regular audits and evaluations need to be performed to confirm that welding activities line up with the suggested WPS guidelines. Furthermore, maintaining thorough records of welding parameters, tools calibration, and inspection outcomes is essential for demonstrating conformity with WPS requirements - welding WPS. By carefully adhering to WPS standards, welders can ensure that their work meets the needed top quality degrees and adds to the general success of the welding task.
Troubleshooting Common Welding Issues
To resolve this, making sure correct cleansing of the base metal prior to welding and making use of the proper protecting gas can considerably minimize porosity. Additionally, distortion, fracturing, and spatter are common welding difficulties that can be alleviated with proper joint preparation, consistent warm control, and Click Here selecting the proper welding consumables. By thoroughly comprehending these usual welding concerns and their root causes, welders can efficiently troubleshoot issues and attain premium welds.
Conclusion
Finally, mastering welding WPS standards calls for a detailed understanding of the standards, utilizing necessary tools, and implementing key techniques for effective welds. Guaranteeing compliance with WPS standards is important for generating quality welds and preventing typical welding issues. By complying with finest techniques and practices, welders can attain reputable and regular outcomes in their welding projects.
In the world of welding, grasping Welding Treatment Specification (WPS) criteria is a critical component see post that directly influences the high quality and honesty of welds.When delving right into the realm of welding techniques, a crucial element to comprehend is the importance and ins and outs of Welding Procedure Specification (WPS) standards. WPS requirements offer a comprehensive standard for welding procedures, making certain consistency, high quality, and safety in the welding procedure. The type of welding maker needed depends on the welding procedure being utilized, such as MIG, TIG, or stick welding.Achieving welding success with the proficiency of vital techniques demands a comprehensive understanding and adherence to Welding Treatment Requirements (WPS) standards.
Report this page